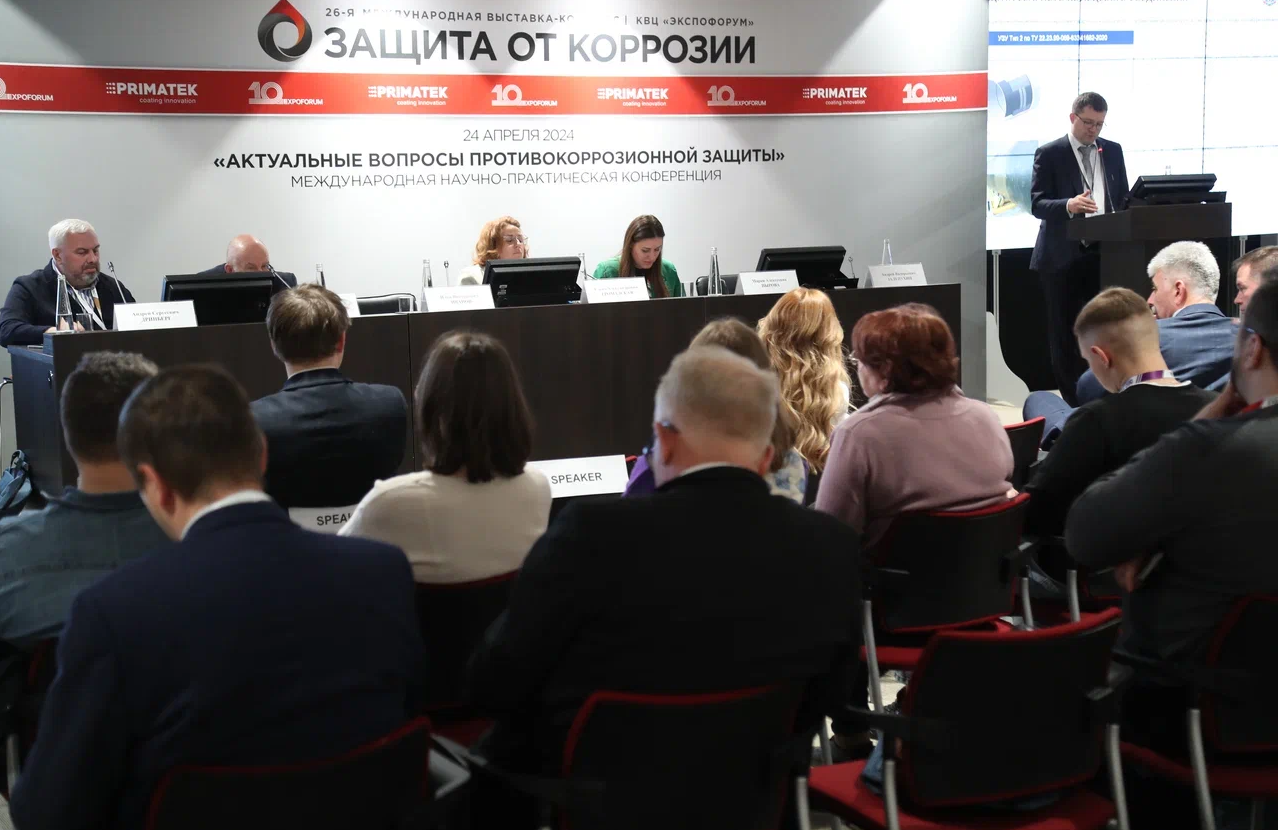
Corrosion of offshore facilities doesn’t just result in hazardous work conditions. Moreover, it adversely affects the country’s economy. Effective solutions of this problem were discussed at the 2nd Session ELECTROCHEMICAL PROTECTION AND OPERATION ISSUES arranged during the international scientific-practical conference TOPICAL ISSUES OF CORROSION PROTECTION.
Andrey Burkov, Adviser to CEO at PSS Corporation, said, ‘Corrosion of vessel hulls and biofouling have been going hand in hand for several thousands of years. As early as in B.C. times, when Romans and Greeks used leaden plates to protect wooden hulks of their ships from worms and mussels, they noticed that the plates fastened with copper nails would rust and come adrift in the attachment points. However, if the nail heads were plated with lead or gold, corrosion would have got far less common. This was how they discovered that metal elements rust in sea water and started to use the passive electrochemical protection method. Later, as the electrical engineering science developed, people found other means of corrosion protection. This area of knowledge got known as electrochemical protection.’
According to the data provided by Prometey Central Research Institute of Structural Materials, in 25 years of operation corrosion of icebreaker plating used in northern regions can reach 4.5 mm. However, with electrochemical protection means applied, this value can be reduced to 0.15 mm. It should be mentioned that 15% of corrosion process are caused by micro organisms. ‘Bacteria literally eat metal. What they excrete after they are full deteriorates the hulls even further,’ Andrey Burkov mentioned.
The expert outlined five effective methods of corrosion protection for the ship-building industry, which he believes should be used together. They are painting, sacrificial anode protection, active cathodic protection with potential adjusted superimposed current, propeller-rudder system protection, and protection of outboard fittings from biofouling.
Vyacheslav Pershukov, Deputy CEO for Development at Chemservice, made a report about working on the interstate standard about anodes of cathodic protection facilities for sea waters and saline media. As he explained, this document will be used to regulate corrosion protection for oil and gas transportation pipelines, as well as mooring and hydrotechnical harbor installations. It will comprise requirements to technical specifications of cathodes, feedstock, and materials used to make them, along with some other parameters.
According to the expert, every anodic material with the highest possible resistance has its pros and cons. For instance, magnetite offers low cost and quite high accessible current intensity, has no voltage restrictions, and can be operated at subzero temperatures. Metal-oxide covered materials have relevantly low dissolution rate, high accessible current intensity, average cost – but they also have temperature restrictions.
‘This is why we should choose such coatings very carefully, as in 90 percent of Russian seas water cools down to minus 3 degrees in winter. We need all-the-year-round protection, and the temperature factor can not only blunt the effectiveness of such coatings but also decrease their life manifold,’ Vyacheslav Pershukov commented. Materials covered with catalytic metals have all the benefits of the previously mentioned category but are also not highly responsive to low temperatures. Yet, as outlined by the expert, they are rather costly.
According to Nikolay Glazov, Senior Researcher at the Technical Survey Department of Transneft R&D, climatic and seasonal factors limit control potential as regards to technical condition of protective coatings and electrochemical protection means of ships on the ‘as needed’ basis. That is why distant control and automated inspection technologies should be preferred.
Participants of the session were also presented corrosion protection equipment for pipelines, marine and mooring facilities produced by Pipeline Systems and Technologies. These were insulating monolith sleeves, subsystems of corrosion monitoring, small-sized cathodic protection plants, anodic ground terminals, dedicated software etc. Alexander Shnyrev, Manager of the Marketing and Sales Department at Pipeline Systems and Technologies, shared information about their key properties.